Bitumen applied as a binder in road construction, requires it to behave as a liquid during its application. Most commonly, this is achieved by heating bitumen to temperatures above 100–200° C until it becomes fluid enough to mix with aggregate, resulting in ‘Hot Mix Asphalt (HMA)’. Other than heating, there are at least two other ways in which bitumen can be made to behave as a liquid at lower ambient temperatures. One option is to dilute bitumen with petroleum solvents like kerosene, naphtha, etc. until it becomes fluid enough for application; the final strength of the material develops when the solvent evaporates. Another option is to emulsify bitumen where bitumen is liquefied by dispersing it in water. The subsequent sections of this article provide a high-level overview of the theoretical concepts, production, classification, and usage of bituminous emulsions in road construction.
In road construction applications, bitumen emulsions provide a safer and environmentally friendlier system than hot bitumen by avoiding the risks of fire, burns, etc., and by using less energy in processes and by reducing emissions. Bitumen emulsions are used widely in road construction mostly in road maintenance and repair works in the form of slurry seals, surface dressing, etc., and in structural pavements in the form of prime and tack coats, cold mixes, recycled asphalt mixes, etc.
Before we proceed more into bituminous emulsions, let's first look at some of the basics of emulsions in general.
What is an emulsion?
An emulsion in simple terms is a dispersion of small droplets of one liquid in another liquid. While emulsions can be formed by any two immiscible liquids, in most emulsions, one of the phases is water.
Before we explain more about emulsions, we need to first understand what the term ‘phase’ means in chemistry. A ‘phase’ is defined as a mechanically separate, homogeneous part of a heterogeneous system. For example, when bitumen is added to water, bitumen is not mixed in water, instead, it is held in suspension. Thus, bitumen and water are part of a two-phase system.
Emulsions may be of oil-in-water (O/W) type, water-in-oil (W/O) type, or a multiphase emulsion such as O/W/O, etc. In oil-in-water (O/W) emulsions the continuous phase is water and the disperse or droplet phase is a water-insoluble ‘oily’ liquid, whereas, in water-in-oil (W/O) emulsions, the continuous phase is an oil and the disperse phase water. W/O emulsions are sometimes called ‘inverted emulsions. In multiple-phase emulsions, the dispersed droplets themselves contain smaller droplets of a third phase, usually the same liquid as the continuous phase. Bitumen emulsions are generally of the O/W type.
Oil and water may form an emulsion through thorough mixing, but will quickly separate when mixing is stopped. For emulsions to be stable, they should contain a third component, the emulsifier, which prevents or retards the separation of the phases.
What are bituminous emulsions?
Bitumen emulsions are usually dispersions of minute droplets of bitumen in water. The droplets normally range from 0.1 to 20 microns in diameter. Thus, emulsification involves the break-up of bitumen into droplets. The bitumen content in bitumen emulsions is varied to suit different requirements and typically varies between 30% and 70%.
A bituminous emulsion essentially consists of three basic ingredients - asphalt binder or bitumen, water and an emulsifying agent. In some cases, the emulsions may also contain additives such as stabilizers, antistrips, break control agents etc.
The internal cohesion and viscosity of the bitumen and the surface tension forces resist the creation of a new interface which essentially opposes the emulsification process. Added to it is the tendency of droplets to coalesce or rejoin. It is necessary to apply mechanical energy in the right way in order to create small drops of bitumen, and once formed, its coalescence shall also be prevented. Thus, the droplets must be stabilized against coalescence by preventing them from getting very close together. Emulsifier added and adsorbed at the surface of droplets provides an electrical and steric repulsion energy barrier which helps prevent the close approach of the droplets. Even if this energy barrier is overcome and the droplets flocculate, the film of the emulsifier on the surface still inhibits coalescence.
Settlement, shear, and boiling or freezing of the emulsion can result in flocculation and coalescence. Flocculation and coalescence may also be initiated by contact with minerals. Bitumen emulsions will contain more emulsifiers than what is necessary to fill the interface, known as free emulsifiers. This ‘free’ emulsifier will help provide good stability and the right performance properties and prevent coalescence during emulsification, storage, and transport.
More on emulsifiers and the process of emulsification
An emulsifier generally consists of two portions - a lipophilic or oil-loving portion and a hydrophilic or water-loving portion. A typical emulsifier has a hydrophilic ‘head’ group and a hydrophobic (lipophilic) ‘tail’. At the bitumen water interface, the emulsifier orientates with the hydrophobic portion in the bituminous phase (oil) and the head group in the water phase. Emulsifiers are derived from fats, vegetable oils, fats, lignin, etc.
An emulsifier molecule is much smaller than a bitumen droplet and it requires thousands of emulsifier molecules to stabilize each droplet. control agents etc.
Emulsifiers prevent bitumen particles to come close together (thereby preventing coalescence) by imparting a charge to the bitumen droplets, thereby repelling the droplets once they approach each other. There is also another stabilization mechanism where coalescence is prevented by a physical hindrance to the close approach of the droplets (with very large molecules like polymers, proteins, etc.). Emulsifiers with large hydrophilic portions may prevent the close approach of the droplets simply by their space-filling properties (steric repulsion).
Cationic vs Anionic Bitumen Emulsions
As discussed, the coating of the bitumen particles by the emulsifier gives them an electrostatic charge. Depending on the type of emulsifier, this can generally be either negative or positive. Emulsions in which the bitumen droplets are negatively charged are called anionic emulsions. Emulsions in which the droplets are positively charged are called cationic emulsions.
Bituminous Emulsions are classified into three categories - anionic, cationic and nonionic. In practice, the first two types are more widely used in road construction and maintenance.
The emulsifiers used to make anionic emulsions are typically prepared from fatty acids by reaction with a strong base such as sodium hydroxide or potassium hydroxide. The resultant fatty acid salt imparts a negative charge to the surface of the bitumen droplets in an emulsion.

Cationic emulsifiers are usually prepared from fatty amines by reaction with a strong acid such as hydrochloric acid. Fatty amine salts impart a positive charge to the surface of the bitumen droplets in an emulsion. pH has an important role in ensuring that the emulsion remains either anionic or cationic. Typically, an anionic emulsion has an alkaline pH of over 7 and a cationic emulsion has an acidic pH of below 7.
How is bituminous emulsion manufactured?
Bitumen emulsions are usually made using a colloid mill. In the colloid mill, hot bitumen is sheared rapidly in water containing an emulsifying chemical agent (emulsifier). This results in the production of very small particles of bitumen dispersed in water (continuous phase). The bitumen particles in suspension do not readily coalesce due to the presence of the emulsifier, which will get concentrated on the surface of the bitumen particles.
During the application of emulsion in road construction, the water in a bitumen emulsion is either lost by evaporation or may separate from the bitumen because of the chemical nature of the surface to which the emulsion is applied. This process is referred to as breaking.
Bitumen emulsion is manufactured either in a batch process plant or in an in-line process plant.
Batch Process - The batch process essentially involves two processes - water phase (soap) preparation followed by the actual emulsion production. The water phase is prepared by mixing accurately metered heated water, emulsifier, and other emulsion chemicals in a tank resulting in the formation of a properly mixed solution. This is followed by the emulsion production process in which the pre-made water phase and bitumen are dosed and added to the colloid mill resulting in the production of bituminous emulsion. If a solvent is to be added to the bitumen, then a batch tank is needed for bitumen, or the solvent must be dosed in-line. In the batch plant process, manual process control is possible as emulsion production involves only a few material flows.
Inline Process - In the in-line process, no batch tanks. Material dosage, water heating, etc. are done continuously using individual dosage pumps for each material. The design of the water phase system will be such that, sufficient reaction time is provided for the chemicals before the water phase meets the bitumen. Also, since the process is inline and continuous, the process needs to be automatically controlled using flow meters for all material dosages.
Breaking and Curing of Bituminous Emulsions
Bitumen emulsions are required to remain stable so that they can be transported, stored, and handled easily. At the same time, they must be made to separate or "break" when it comes into contact with aggregates or other pavement surfaces during road construction. This process of ‘breaking’ is crucial in enabling bituminous emulsions to become a continuous bitumen film in order to fulfill their role as a binder in road materials or as protective coatings. The speed of this setting and curing process depends on the reactivity of the emulsion, the reactivity of the aggregate, and environmental conditions such as temperature and humidity.
Breaking of anionic emulsions in normal use is essentially caused by loss of water, e.g. evaporation, causing coalescence. Cationic emulsions also break for the same reason, but the positive charge on the dispersed bitumen particles can react with the predominantly negative surface charge on most aggregates giving a more rapid break and good adhesion.
Aggregates take up a characteristic surface charge which depends on pH and the nature of the minerals that are present in it. Silicious aggregates which are high in silica tend to take up a negative charge, whereas basic aggregates like limestones can take a positive charge. Thus, cationic emulsions react faster with an aggregate with a negative surface charge.
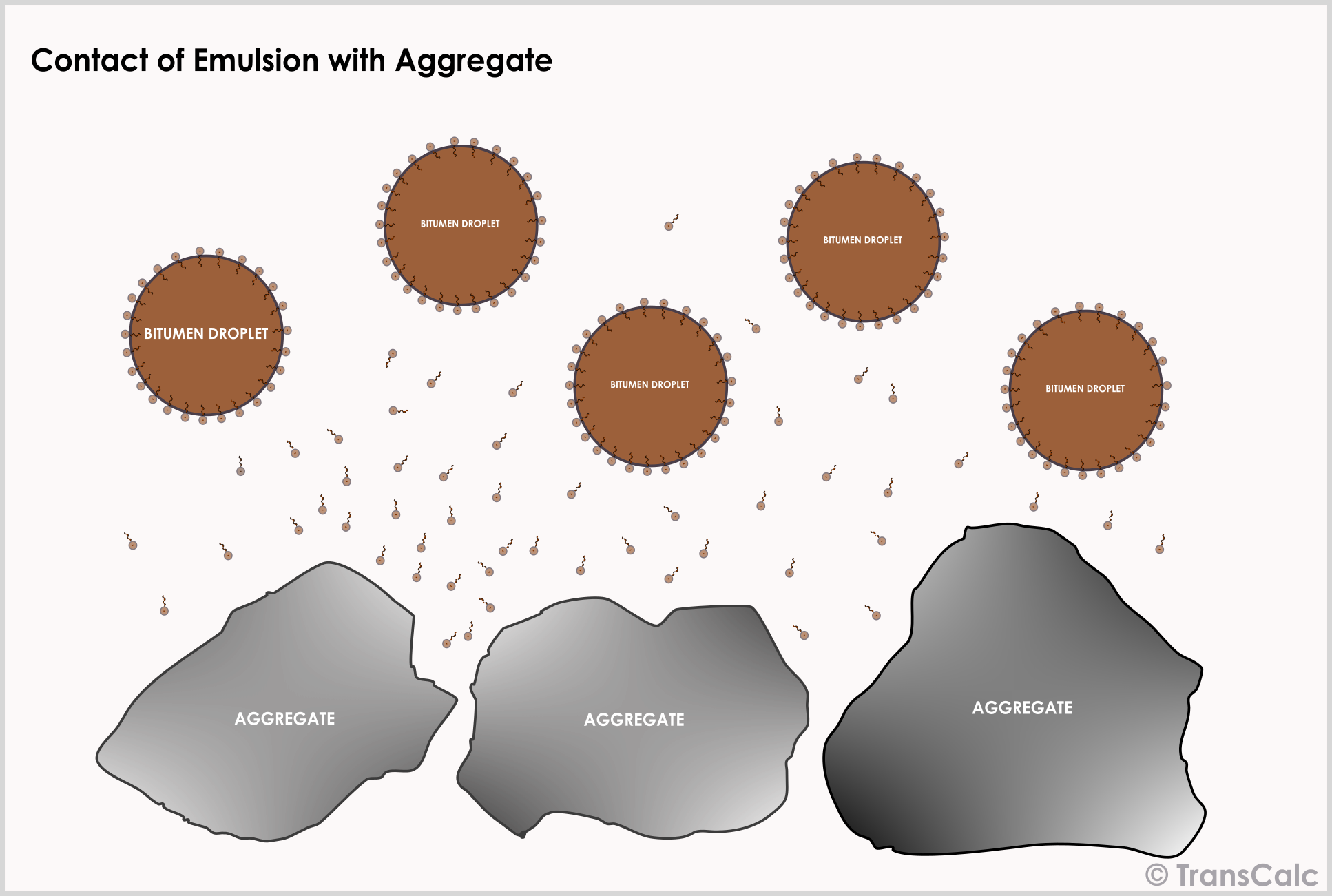
The first stage in the breaking and curing process involves the adsorption of the emulsifier onto the aggregate surface. While free emulsifier gets adsorbed rapidly; emulsifier is abstracted from the bitumen water interface much more slowly. Cationic emulsifiers adsorb much more strongly on siliceous minerals than anionic or nonionic emulsifiers.
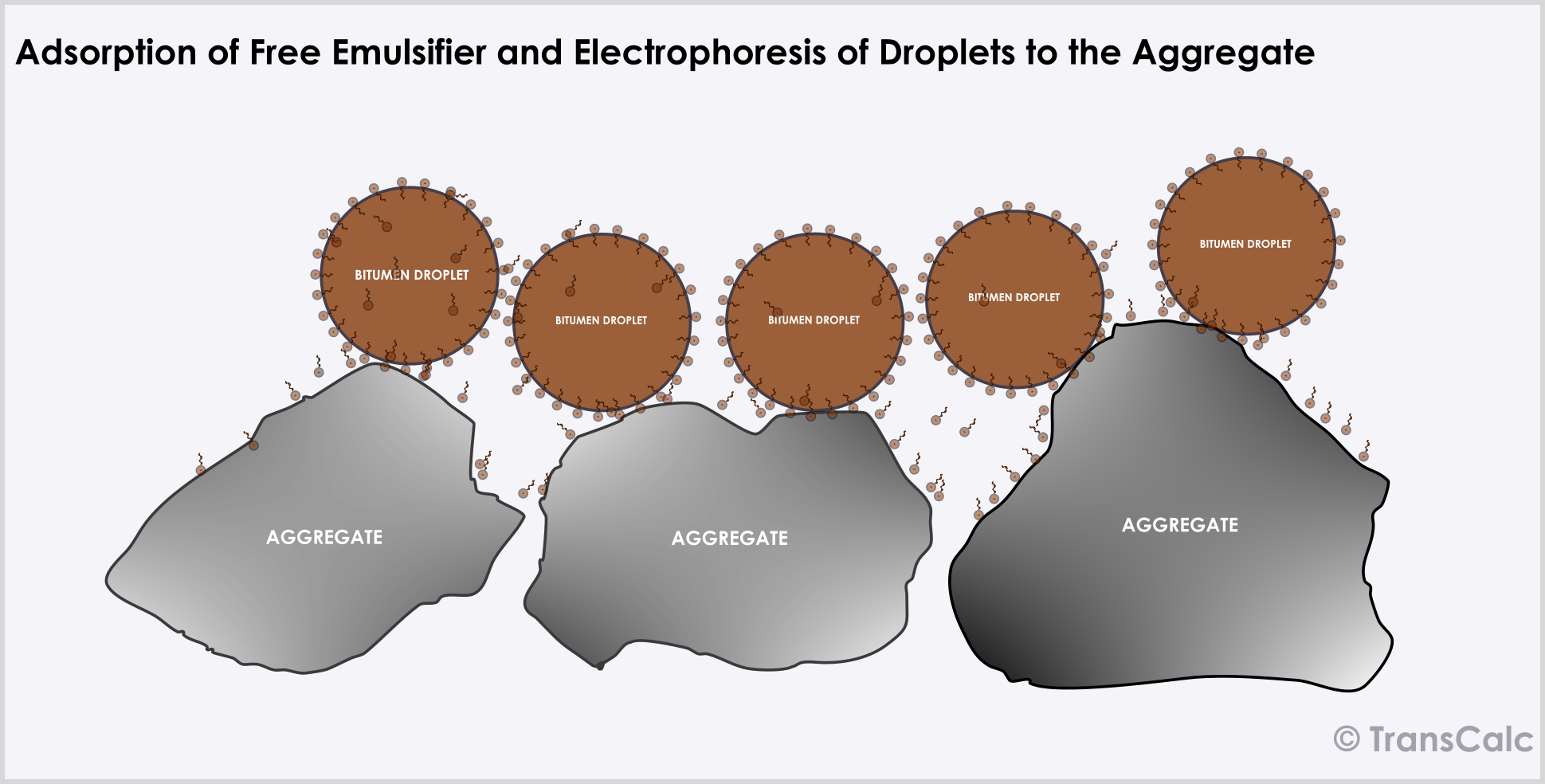
The droplets of bitumen in the emulsion have a small charge and move towards an aggregate surface with the opposite charge (electrophoresis). Which results in its concentration at the aggregate surface. This brings the particles closer together leading to flocculation, coalescence, and spreading over the surface. The water eventually leaves the system by evaporation resulting in the concentration of droplets and its coalescence.
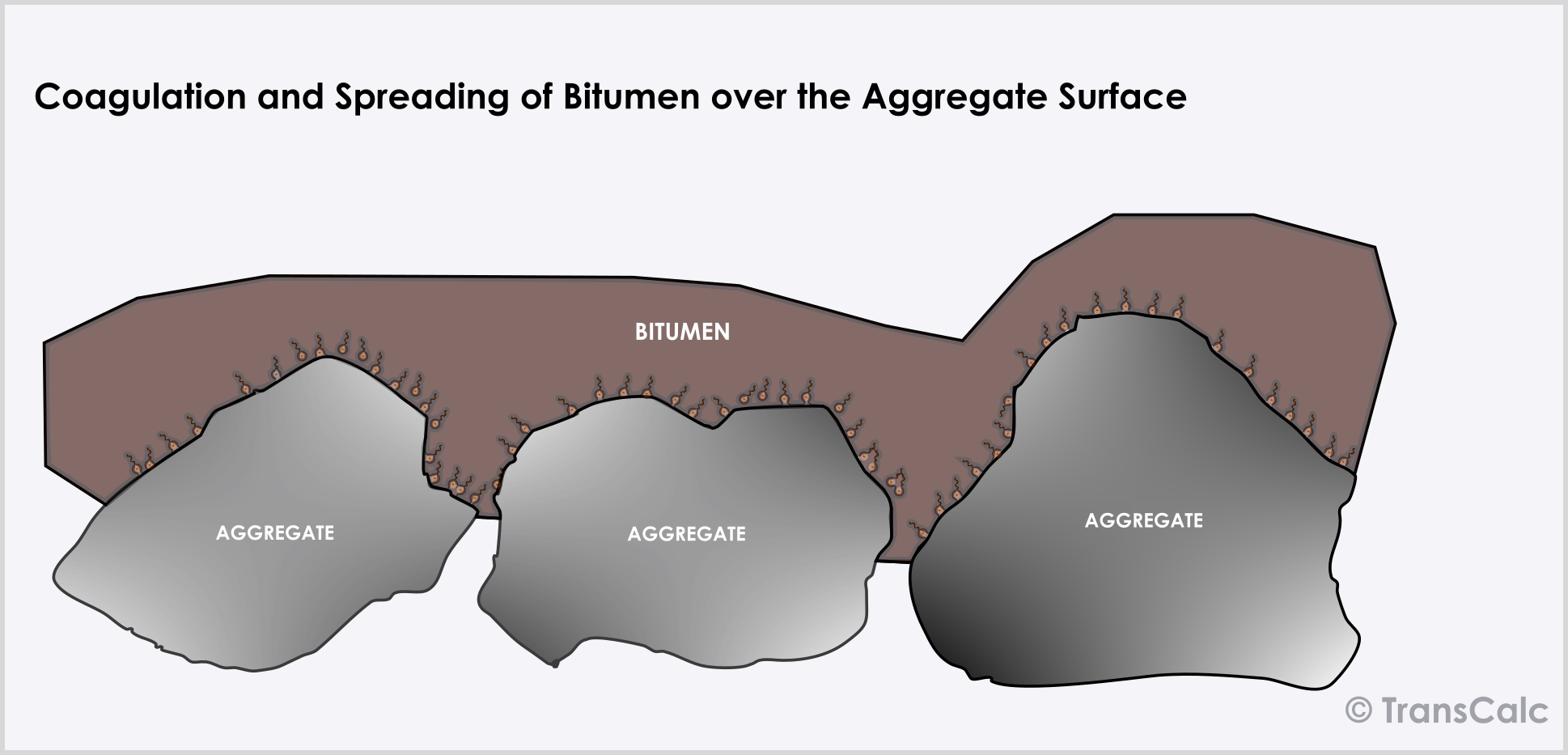
Types of Bituminous Emulsions
The two most common basic emulsion types are cationic (C) and anionic (A) emulsions. Their setting characteristics are defined in terms of rapid (R), medium (M), and slow (S) setting. Rapid setting emulsions set quickly in contact with clean aggregates of low surface area. Medium-setting emulsions set sufficiently less quickly that they can be mixed with aggregates of low surface area. Slow-setting emulsions will mix with aggregates of high surface area. Slow-setting emulsions are more stable than medium-setting emulsions which, in turn, are more stable than rapid-setting emulsions.
In the United States (as per ASTM and AASHTO classification), paving-grade asphalt emulsions are classified by an alphanumeric designation (CSS-1h, CSS-1, RS-1, MS-1, SS-1h, etc.). The terms RS, MS, SS, and QS indicate how quickly the asphalt droplets in the emulsion will coalesce or revert to asphalt cement with the term RS indicating 'Rapid Setting', MS indicating 'Medium Setting', SS indicating 'Slow Setting' and QS indicating 'Quick Setting' respectively.
The presence of the letter 'C' in front of the emulsion type denotes cationic emulsion while the absence of 'C' denotes anionic emulsion. Thus RS-1 is anionic while CRS-1 is cationic. The numbers in the classification indicate the relative viscosity of the emulsion. Thus CRS-2 is more viscous than CRS-1. In certain emulsion grades (CSS-1h, HFMS-2s, etc.), letters 'h' and 's' are added to indicate the presence of a harder (h) and softer (s) base asphalt respectively. The term 'HF' precedes some anionic grades which indicate high float as measured by the float test.
Applications of Bituminous Emulsions
Bituminous emulsions are used in a wide range of applications in road construction varying from their use as bond coats to cold-in-place recycling and even in soil stabilization applications.
Bituminous emulsions are used as such without any addition of mineral aggregates as is the case with tack coats prime coats, fog seals, etc., and in pavement repair applications such as crack sealing, bond material during pothole repairs, etc. Bituminous emulsions in combination with graded aggregates, mineral fillers, additives, water, etc. are being widely used worldwide for various surface treatment applications such as single and double surface treatments, cape seals, slurry seals, micro-surfacing, seal coats, etc., and in soil stabilization, construction of Emulsion Treated Bases (ETB), Bitumen Stabilized Mixes (BSM), etc. The use of bituminous emulsions in asphalt recycling applications is gaining popularity in recent years as a result of its successful application in both in-situ and in-plant cold recycling projects including Full Depth Reclamation (FDR) projects.